3-Axis vs 5-Axis Machining: A Comprehensive Guide to Making the Right Choice
Learn the key differences between 3-axis and 5-axis machining, their applications, benefits, and how to choose the right CNC technology to enhance your production efficiency and meet complex manufacturing demands.
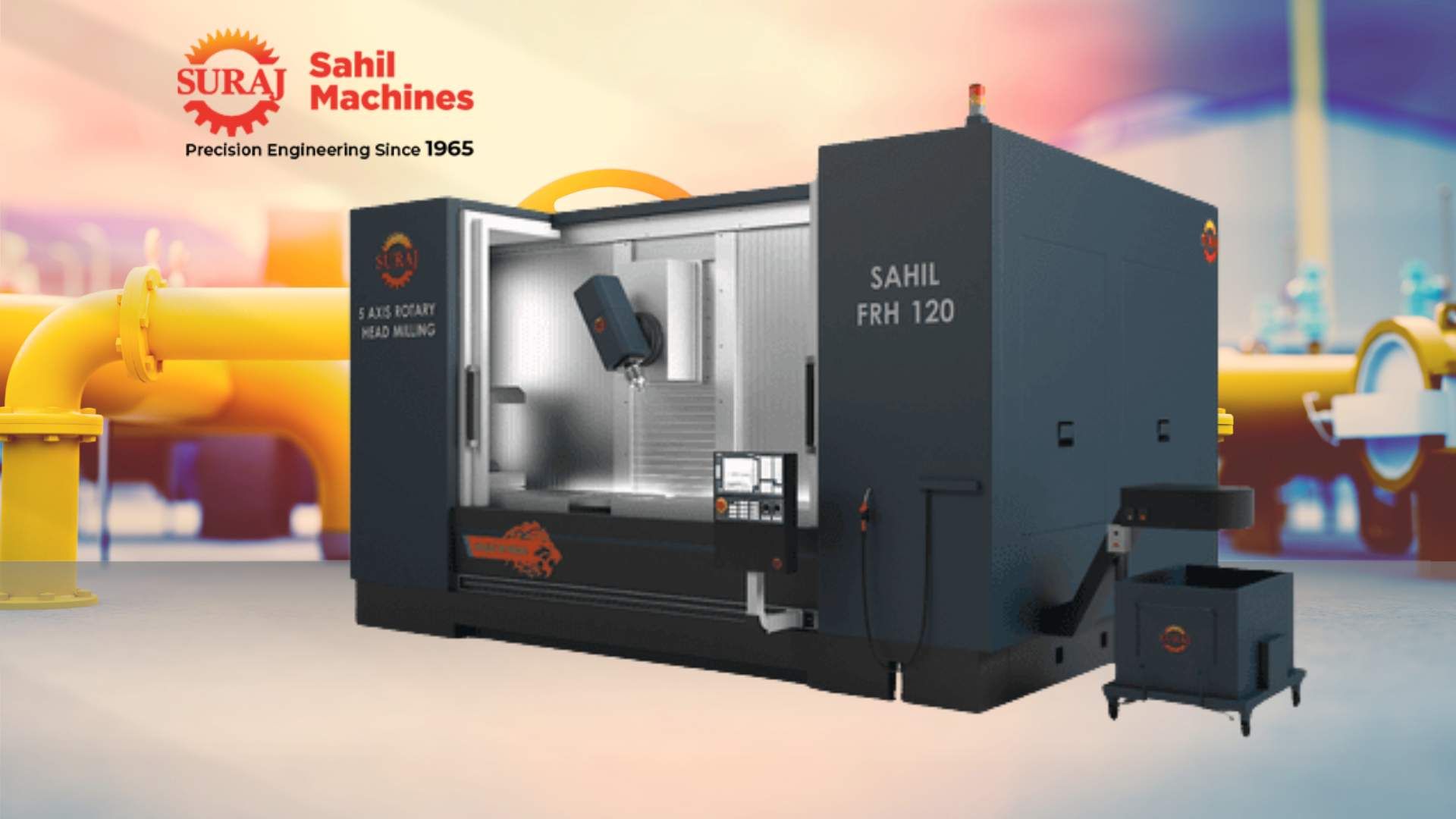
April 01, 2025
Share:
In the current competitive manufacturing landscape, production efficiency is what will keep you at the top. Choosing the right CNC machining technology for your industry can be a difficult task. Let's review some of the key differences between 3-axis and 5-axis machining so you can make an informed decision. Whether you want to upgrade or get a new CNC machine, keeping yourself informed always helps you choose the best for your manufacturing needs.
What is 3-Axis Machining?
As its name suggests, the machine operates along the three linear axes, X, Y, and Z. The cutting tool of a 3-axis machining tool moves along the three linear directions and pretty much has a traditional approach that has been there for quite a few years.
The machining operations offered by a 3-axis machine are basic and include:
- Creating simple geometries
- Performing milling and drilling operations
- Manufacturing high-volume simple designs and components
Explore our range of 3-axis CNC machines to see how they can enhance your production efficiency.
What is 5-Axis Machining?
5-axis machining is designed to create complex and intricate geometries. It elevates machining by adding two more axes (A and B) to the standard three axes (X, Y, and Z). This design gives extended movement, making it a great tool for achieving superior surface finishes.
The machining operations offered by a 5-axis machine are advanced and include:
- Creating complex geometries in one setup
- Easy access to inaccessible surfaces
- Providing superior surface finishes
- Reducing production time significantly
From aerospace to automotive, major industries require intricate geometries. These industries work on high tolerances, and a 5-axis machining center can approach workpieces from any angle, making it a suitable tool in the manufacturing sector.
Discover our advanced 5-axis CNC machines designed for precision and complex geometries.
Key Differences Between 3-Axis and 5-Axis Machining
Precision and Complexity
- 3-Axis Machines: Can accurately manufacture less complex parts.
- 5-Axis Machines: Create complex geometries with tighter tolerances, allowing for more precise tool positioning and better surface finishes.
Setup and Efficiency
- 3-Axis Machines: Require multiple setups for complex parts.
- 5-Axis Machines: Reduce setup time, allowing tasks to be completed in a single setup. This translates to:
- Reduced labor costs
- Fewer opportunities for error
- Increased production throughput
- Better consistency across parts
Cost Considerations
- 3-Axis Machines: Lower initial investment.
- 5-Axis Machines: Higher initial investment but offer:
- Decreased setup and production time
- Reduced material waste
- Lower labor requirements
- Ability to take on more complex, higher-margin projects
For a detailed comparison, check out our CNC technology insights.
Is It Worth the Upgrade?
Understanding Your Current Production
If your shop primarily handles simple geometries and standard parts, your current 3-axis setup may be perfectly adequate. However, if you're regularly encountering complex components or finding yourself limited by your current capabilities, 5-axis machining could transform your operation.
Learn how CNC machines can impact production efficiency.
Planning for Growth
The decision to invest in 5-axis machining isn't just about current needs - it's about future opportunities. Many manufacturers find that 5-axis capabilities open doors to new markets, allowing them to take on more sophisticated, higher-margin projects.
ROI Potential
While the investment in 5-axis technology is substantial, the potential returns are compelling:
- Increased productivity through reduced setups and faster cycle times
- Access to higher-value projects and new market segments
- Lower operational costs through improved efficiency
- Enhanced competitive position in the marketplace
Looking to the Future
The manufacturing landscape continues to evolve, with increasing demand for complex, precise components. While 3-axis machining remains viable for many applications, 5-axis technology represents a significant step forward in manufacturing capability.
The decision to upgrade should be based on a careful analysis of your business needs, financial position, and growth objectives. The right choice will depend on your specific circumstances, but understanding the full scope of possibilities will help you make an informed decision that serves your business well in the years ahead.
Contact us to discuss your CNC machining needs or learn more about upgrading to 5-axis technology.
Remember: This isn't just a technology upgrade - it's an investment in your company's future competitive position. Take the time to evaluate thoroughly, but don't let fear of change prevent you from making a strategic move that could elevate your business to the next level.
FAQ
5-axis machines have a higher initial investment cost, but they offer long-term savings through reduced setup time, faster production, and the ability to take on high-margin projects. 3-axis machines are more affordable upfront but may require more manual intervention for complex parts.
While some 3-axis machines can be upgraded with rotary tables or trunnion attachments to add additional movement, they won't fully replicate the capabilities of a dedicated 5-axis machine. If you require true 5-axis functionality, investing in a dedicated 5-axis CNC is recommended.
Assess your current and future production needs. If your business is handling complex components, experiencing long setup times, or missing out on high-value projects due to machine limitations, upgrading to a 5-axis CNC could significantly boost efficiency and profitability.
Follow Us:
Latest Posts
Get in touch with us about anything.
Connect with our team to explore the alloy solutions and machinery expertise you need.