CNC Vertical Turn-Mill Machines: Revolutionizing Pump Manufacturing for Precision and Efficiency
CNC Vertical Turn-Mill Machines are revolutionizing pump manufacturing by combining turning and milling in one setup, optimizing production with high precision and efficiency. These advanced machines enable the production of intricate pump components, such as impellers, shafts, and casings, ensuring consistent quality and improved performance. With cutting-edge technologies like multi-axis machining, IoT connectivity, and automated tool changes, CNC Vertical Turn-Mill Machines are setting new standards for productivity and innovation in the pump industry
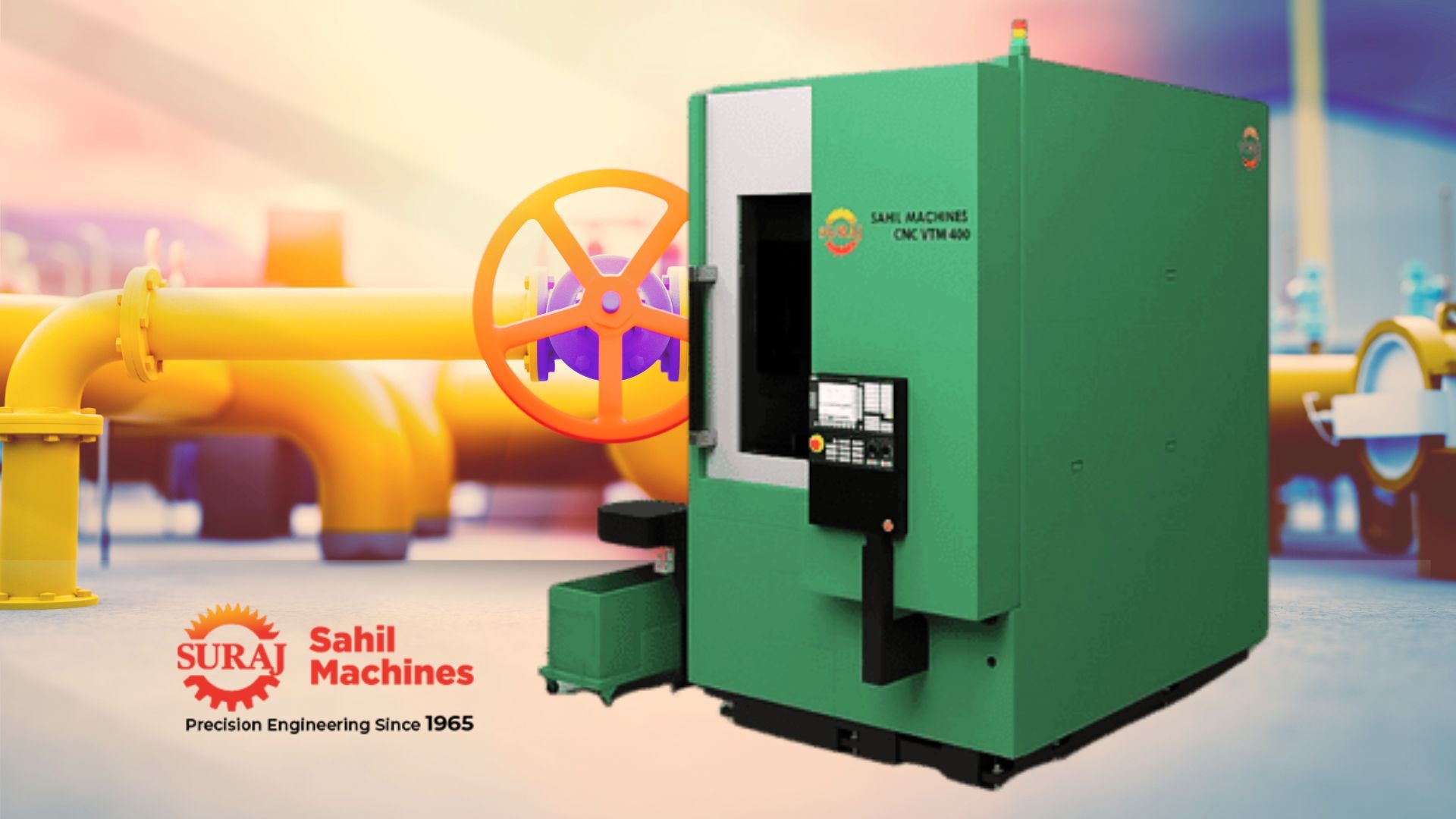
April 01, 2025
Share:
Incorporating changes into the ever-evolving world of industrial manufacturing, vertical CNC turn-mill machines have become instant game-changers, very much so in the pump industry. Advanced, multi-functional machines, integrate the capabilities of vertical turning lathes with those of milling machines, offering unparalleled precision, efficiency, and versatility. In this overall guide, take a look at how these machines are changing manufacturing in pumps, salient features of the machines, and recent technological advances driving innovation in vertical stone milling machines.
CNC vertical turn-mill machines are highly advanced pieces of equipment that integrate turning and milling operations in a single setup. This said machinery, with controlled movements and operations given to it by the computer numerical control, better known as CNC, can enable the production of complicated parts with great accuracy.
1. Smooth Production by Integrated Operations
CNC vertical turn-mill machines dominate because they have perfectly integrated turning and milling operations into one machine. This greatly reduces set-up times and also eliminates the need for a number of machines, therefore smoothing the entire manufacturing process. Since each operation is conducted in one setup, a manufacturer can rationalize their workflow to optimize their productivity by reducing costs.
2. Milling of Complex Geometries with Multiple Axes
Unique among machines with this feature, most of them have the capability for multi-axis machining, some up to 5-axis. This opened up possibilities for making intricate geometries and complex shapes essential in high-performance components. Such multi-axis CNC machining enables making the details of parts like impellers featuring curved vanes in a single setup feat of versatility and efficiency.
3. Live Tooling for More Versatility
Further enhancements are provided to CNC vertical turn-mill machines by the live tooling feature, which could perform milling, drilling, and tapping while the workpiece is in a stationary position. It acts like a multifunctional tool that increases versatility, reducing the need for multiple setups. This translates to higher production times with higher flexibility in operations that manufacturers get.
4. Maximising Efficiency
Efficiency is additionally enhanced by the use of automatic tool-changing systems that enable the machine to change from one cutting tool to another in only a matter of seconds, all by itself. This feature of turning without any delay for tool change will not only increase productivity but also maintain consistent quality during the machining until the production volume becomes high.
5. Precision in the Making of Components
The pillars of these machines are precision, given that their CNC control permits tight tolerances and exact dimensions so vital in the making of components like impellers and pump shafts. The accuracy possible with CNC vertical turn-mill machines is essential to meeting modern pump performance requirements, which are very unforgiving toward even minor deviations.
6. Vertical for Stability and Superior Finish
While very similar in function, these vertical machines boast additional advantages for large or heavy workpieces. The vertical spindle hence offers great stability, while the design brings in proper chip evacuation for a neat job in cutting with a superior surface finish. Therefore, CNC vertical turn-mill machines are reliable and can be depended upon for high-quality, precision-focused manufacturing.
Applications in the Manufacturing of Pumps
CNC vertical turn-mill machines have completely revitalized the manufacturing process of various pump parts. Herein, are the main applications:
1. Manufacture of Impellers
In that regard, impellers play a significant role in transferring energy from a motor to a fluid. CNC vertical turn-mill machines manufacture impellers with profoundly exacting blade profiles that optimize the fluid flow and minimize turbulence. Having multi-axis capability, these machines manufacture complex curved surfaces with intricated vane geometries that improve the efficiency and performance of pumps. For centrifugal pumps, such precision manufactures impellers that improve energy efficiency and operational effectiveness.
2. Shaft of pumps
Precision related to the pump shaft is very important from a holistic point of view about the performance and life of a pump. The shaft can be manufactured on CNC vertical turn-mill machines, starting from rough bars to perfectly balanced shafts in one setup. These machines are designed to conduct a number of operations, such as turning, milling, and keyway cutting, without transferring the workpiece. This nets highly accurate shafts with superior surface finishes, cutting down friction and wear, enhancing pump life, and unmistakably reducing maintenance costs.
3. Volute casing
The fluid is guided by a spiral casing and converts velocity to pressure. A single setup can generate complex internal flow paths and external mounting features with a CNC vertical turn-mill machine. Their precision enables engineers to design innovative volute casings, which optimize fluid flow with structural integrity. These machines make residential or industrial pumps far easier, allowing the manufacture of high-efficiency casings.
4. Diffusers and Guide Vanes
The diffusers and guide vanes are critical for slowing the fluid, hence converting kinetic energy to pressure. CNC vertical turn-mill machines ensure high accuracy in machining at the diffuser vanes for minimum turbulence and assurance of maximum fluid flow. These machines hold tight tolerances across complex geometries. This ensures the consistency of the performance of the vanes, leading to increased efficiency with better energy consumption, whether for small residential or big industrial pumps.
5. Seals and Bearings
Housings Seal and bearing housings depend on leak-free operation and smooth pump running. The high precision to be provided for the perfect sealing surface in seal housings or the correct positioning in bearing housings is offered by CNC vertical turn-mill machines. A high degree of precision minimizes the risk of an occurrence of leak and vibration, which normally increases the service life of bearings. One-setup turning and milling offers great accuracy, which, in fact, plays a great role in industries like chemical processing and the oil and gas industry.
Advantages OF CNC Vertical Turn-mill Machines in the Pump Industry
The valuable advantages of adopting CNC vertical turn-mill machines for the fabrication of pumps are great and changed the industry's face. Herein, key benefits are broken down as follows:
1. Efficiency These CNC vertical turn-mill machines reduce operations by completing complicated pump parts in one setup instead of using several machines. Such consolidation cuts set-up times and shortens production cycles. All this contributes to increased productivity; with faster turnaround times, manufacturers can meet tight deadlines while sustaining product quality.
2. Exactness Precision in the manufacture of pumps means even a minor deviation may become critical. It is possible to achieve consistency and accuracy with CNC machines; therefore, parts to be used, such as impellers and shafts, will be made to tight tolerances. These high levels of precision minimize errors, reduce material waste, and ensure the resultant pumps perform efficiently and reliably.
3. Adaptability CNC vertical turn-mill machines can handle everything from steel to exotic alloys, allowing them to cut through a range of pump types. This would also permit manufacturers to meet upsurges in market demand or special orders more quickly, thereby increasing production flexibility.
4. Cost-effective While the initial investment in a CNC might be higher, there are significant long-term cost savings to be realized. First, it greatly reduces the number of machines required. It reduces labor costs as many operations are automated, thus reducing the overall cost per part. They offer enough precision that results in fewer errors and reduced scrap rates.
5. Quality CNC machines fabricate quality parts with good surface finishes and tight tolerances. The pumps will hence meet or excel in their performance. Consistency in quality raises the satisfaction of customers and the reputation of the manufacturer, reducing warranty claims and defective products.
6. Agility CNC machines enable manufacturers to make quick changes between standardized parts production and custom parts. The rapid setup and programmable controls make changes from large production runs to small batches without huge effort, hence enabling companies to supply to a wide market, including niche markets with specialized industries requiring custom designs.
Advances in Technology and Innovations
Automation and Robotics at Advanced Levels Automation and robotics integration in CNC continuously reduce human interference. Robotic arms perform all the material loading/unloading jobs, while for optimum tool performance, AI-driven tool optimisation is utilised to enhance the quality of parts. Such automation allows manufacturers to run the machines 24/7, increasing overall output in a way that cuts labor costs.
Digital Twins and Simulation Technology Digital twin technologies virtualize real CNC machines for monitoring and optimization in real time. In this way, manufacturers can simulate machining processes, test strategies, and even predict maintenance activities without interfering with production. This reduces errors, improves efficiency, and extends machine life.
**Integration of IoT ** IoT technology empowers CNC machines to connect with an upper level of manufacturing where performance and production can be viewed in real-time. The immediate result of this kind of connectivity is that it can be monitored and controlled remotely, therefore offering huge opportunities for optimization and swiftness in responding to problems by a manufacturer, thereby enhancing efficiency and decision-making.
High-Speed Machining (HSM) High-speed machining technology increases the speed of production while maintaining very high precision. The generated heat is minimized by the use of only a properly optimized spindle speed and appropriate cutting tools, hence improving surface finishes and accuracy in dimensions. This is an important aspect in pump components, such as shafts and impellers, which require tight tolerances.
**Integrating Additive Manufacturing ** Hybrids of both additive and subtractive manufacturing machines open up possibilities for advanced geometries and innovative designs. The machine will help in rapid prototyping or the production of custom parts to shorten development time and reduce time-to-market.
**Advanced Tool Management Systems ** The tool management system integrated into modern CNC machines monitors in real time the wear and damage of a tool. Together with an ATC, the tool usage will be optimized and production time reduced while replication of quality is assured or improved.
**Ultrasonic-Assisted Machining Process ** Machining by ultrasonic assistance reduces cutting forces and provides an improved surface quality for especially hard or brittle materials. The capability of machining thin-walled or light and fragile parts of the pump precisely is allowed with UAM, which can improve pump performance through light yet durable parts.
The CNC vertical turn-mill machines ensure great efficiency, precision, versatility, and profitability in the pumps' manufacturing process. Besides continuous support of automation, integration of IoT, and additive manufacturing, these machines are constantly up-to-date, hence representing one of the main means of modern pumps manufacturing.
The success with the CNC vertical turn-mill machines has opened complete transformation possibilities for the future pump manufacturing business. The smart factories would run around the clock, completely automated, integrating robotics and quality control systems into this productivity boost. Driving this with AI-powered optimization, machines would adapt in real-time, refining processes further to full efficiency and customization, producing less waste, with higher cost-effectiveness.
Advanced on-board inspection systems will implement on-site quality control to ensure near-perfect components. Increasing demands for customized pumps will be met through the seamless integration of CAD/CAM systems that allow for rapid design iteration. As materials science continues in its relentless development, the CNC machines will be working new materials into high-performance, building more durable and more efficient pumps.
The application of CNC vertical turn-mill machines will bring an unparalleled revolution in the manufacturing processes of pump industries, affording precision, efficiency, and sustainability. This no doubt will increase productivity while placing manufacturers in the fore of innovation, marking the beginning of an industrial revolution.
FAQ
Choosing and selecting the right CNC vertical turn-mill machines is your topmost priority. Well, we want the same, for you to have an efficient and fast manufacturing experience. At Sahil Machines, we ensure you receive top-quality products. Backed by years of industry experience, we offer advanced Gantry Milling machines that deliver exceptional precision, reliability, and efficiency, designed to meet the unique demands of your operations. Sahil Machines offers customizable solutions that meet the diverse requirements of customers across industries.
CNC Vertical Turn-Mill Machines integrate both turning and milling operations in one setup, making them highly efficient for complex parts. In the pump industry, they’re used to manufacture components like impellers, shafts, and casings with high precision, reducing production time and improving the performance of pumps.
These machines streamline the production process by combining multiple operations into one setup, cutting setup times, reducing machine requirements, and ensuring high precision. They enhance productivity, improve product quality, and lower overall manufacturing costs.
These machines streamline the production process by combining multiple operations into one setup, cutting setup times, reducing machine requirements, and ensuring high precision. They enhance productivity, improve product quality, and lower overall manufacturing costs.
CNC control allows for tight tolerances and exact dimensions, which are crucial for pump components like impellers and shafts. This precision ensures consistent fluid flow, reduces friction and wear, and minimizes the need for frequent maintenance.
Follow Us:
Latest Posts
Get in touch with us about anything.
Connect with our team to explore the alloy solutions and machinery expertise you need.