Cutting Fluids in Metal Machining: Importance, Benefits, and Best Practices
Learn the essential role of cutting fluids in metal machining, their types, benefits, and best practices. Discover how advanced cutting fluids enhance precision, reduce tool wear, and improve machining efficiency for optimal manufacturing performance.
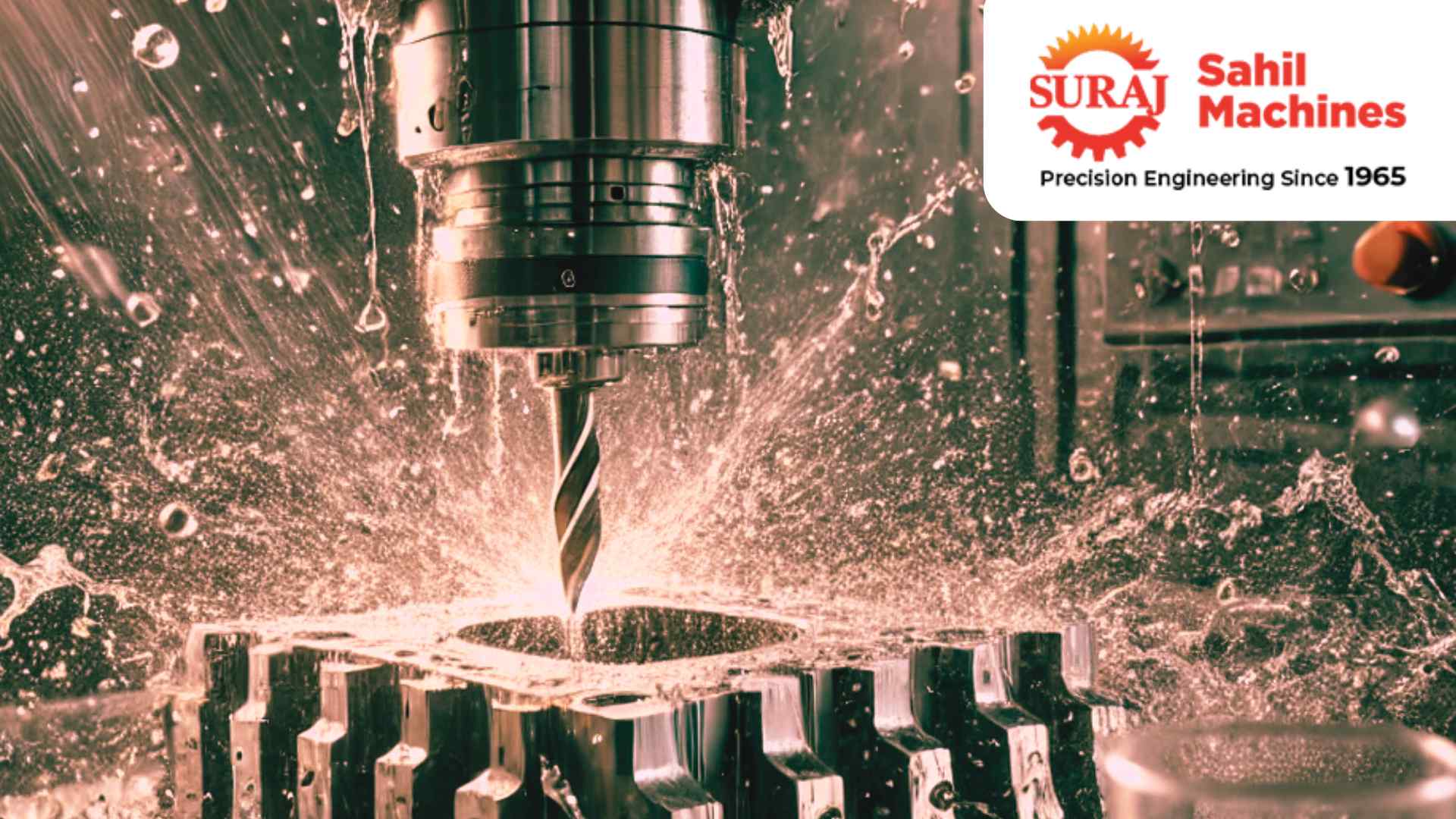
April 01, 2025
Share:
Cutting fluids are the unsung heroes of metal machining in modern manufacturing. Whether you're a seasoned machinist or a newcomer to the industry, understanding the role and correct usage of cutting fluids can significantly impact your machining performance.
Understanding Cutting Fluids: The Basics
Cutting fluids are specialized liquids, oils, or gases designed to enhance machining performance by providing cooling, lubrication, chip evacuation, and corrosion prevention.
In high-precision manufacturing, using the right cutting fluid can be the difference between mediocre and exceptional machining results.
The Challenge: Heat and Friction in Metal Cutting
Metal cutting generates high temperatures and friction, which, if not managed properly, can lead to:
- Thermal expansion and contraction, reducing machining accuracy
- Increased tool wear, raising operating costs
- Poor surface finish, affecting product quality
- Lower productivity, causing inefficiencies
Types of Cutting Fluids: Choosing the Right Solution
Different machining operations require different types of cutting fluids. Let’s explore the main categories:
1. Water-Based Fluids
- High cooling properties
- Ideal for high-speed machining
- Examples: Water-soluble oils, semisynthetics, synthetics
- Suitable for general-purpose cutting tasks
2. Oil-Based Fluids
- Provide excellent lubrication
- Used in heavy-duty machining
- Examples: Straight oils, mineral oils, vegetable oils
- Best for deep cuts and high-pressure operations
3. Gas-Based Fluids
- Latest innovation in cutting fluid technology
- Includes CO₂, compressed air, and Minimum Quantity Lubrication (MQL)
- Eco-friendly alternative for precision machining
Key Benefits of Using Cutting Fluids
Temperature Management
- Proper cooling prevents thermal expansion, maintaining high precision.
- Essential for tight tolerance machining.
Improved Lubrication
- Reduces friction between the tool and workpiece.
- Extends tool life, cutting down operational costs.
Efficient Chip Evacuation
- Removes chips from the cutting zone, preventing tool breakage.
- Ensures better surface finish.
Corrosion Protection
- Protects both tools and workpieces from oxidation.
- Extends machine life and reduces maintenance costs.
At Sahil Machines, we ensure top-quality CNC machines that deliver precision, reliability, and efficiency, designed to meet your manufacturing needs.
Best Practices for Cutting Fluid Application
Success with cutting fluids starts with proper implementation. Here are key best practices:
Selection Criteria
- Match fluid type to workpiece material
- Consider cutting speed and depth requirements
- Ensure tool compatibility
- Check for environmental compliance
Application Methods
- Flood Cooling: Best for large production runs
- Mist Application: Ideal for light machining
- Spray Systems: Provides precision fluid delivery
Maintenance Requirements
- Filter fluids regularly
- Monitor concentration and pH levels
- Replace degraded fluids to maintain efficiency
Future Trends in Cutting Fluid Technology
With Industry 4.0, cutting fluids are evolving to meet sustainability and efficiency needs.
Eco-Friendly Solutions
- Biodegradable fluids using plant-based formulations
- Designed to reduce environmental impact
Industry 4.0-Integrated Smart Monitoring
- IoT sensors analyze fluid usage
- AI-powered optimization ensures efficiency
- Predictive maintenance systems extend fluid life
Minimum Quantity Lubrication (MQL)
- Reduces fluid consumption
- Maintains machining efficiency
- Perfect for sustainable manufacturing
Safety Considerations
While cutting fluids are essential, safety precautions are equally important:
- Ensure proper ventilation in machining areas
- Wear appropriate personal protective equipment (PPE)
- Follow correct disposal procedures
- Keep work areas clean
Conclusion
Cutting fluids are critical to successful metal machining. By understanding their types, benefits, and best application methods, manufacturers can optimize production for better efficiency, quality, and cost-effectiveness.
As technology advances, staying updated on new developments in cutting fluid technology is key to remaining competitive in modern manufacturing.
The right cutting fluid, correctly applied and well-maintained, is an investment in your machining success.
For custom cutting fluid solutions, contact Sahil Machines today!
Related Resources
For more insights on advanced machining solutions, check out our CNC Machining Insights!
FAQ
Yes, they reduce thermal expansion, leading to precise cuts and better surface finishes.
Many modern cutting fluids are biodegradable and designed to minimize environmental impact.
Yes, certain cutting fluids contain additives that protect tools and workpieces from oxidation.
No, but they are essential for high-speed and precision machining to ensure optimal performance.
Regular monitoring is required. Change fluids when they become contaminated, ineffective, or degraded.
Maintain proper concentration levels and filter out contaminants regularly. Use biocides to prevent bacterial growth
Follow Us:
Latest Posts
Get in touch with us about anything.
Connect with our team to explore the alloy solutions and machinery expertise you need.