How Robotic Arms Are Revolutionizing CNC Machine Automation
Robotic arms are redefining CNC machine automation by enabling round-the-clock productivity, enhanced precision, and improved safety. Learn how this powerful combination is shaping the future of manufacturing.
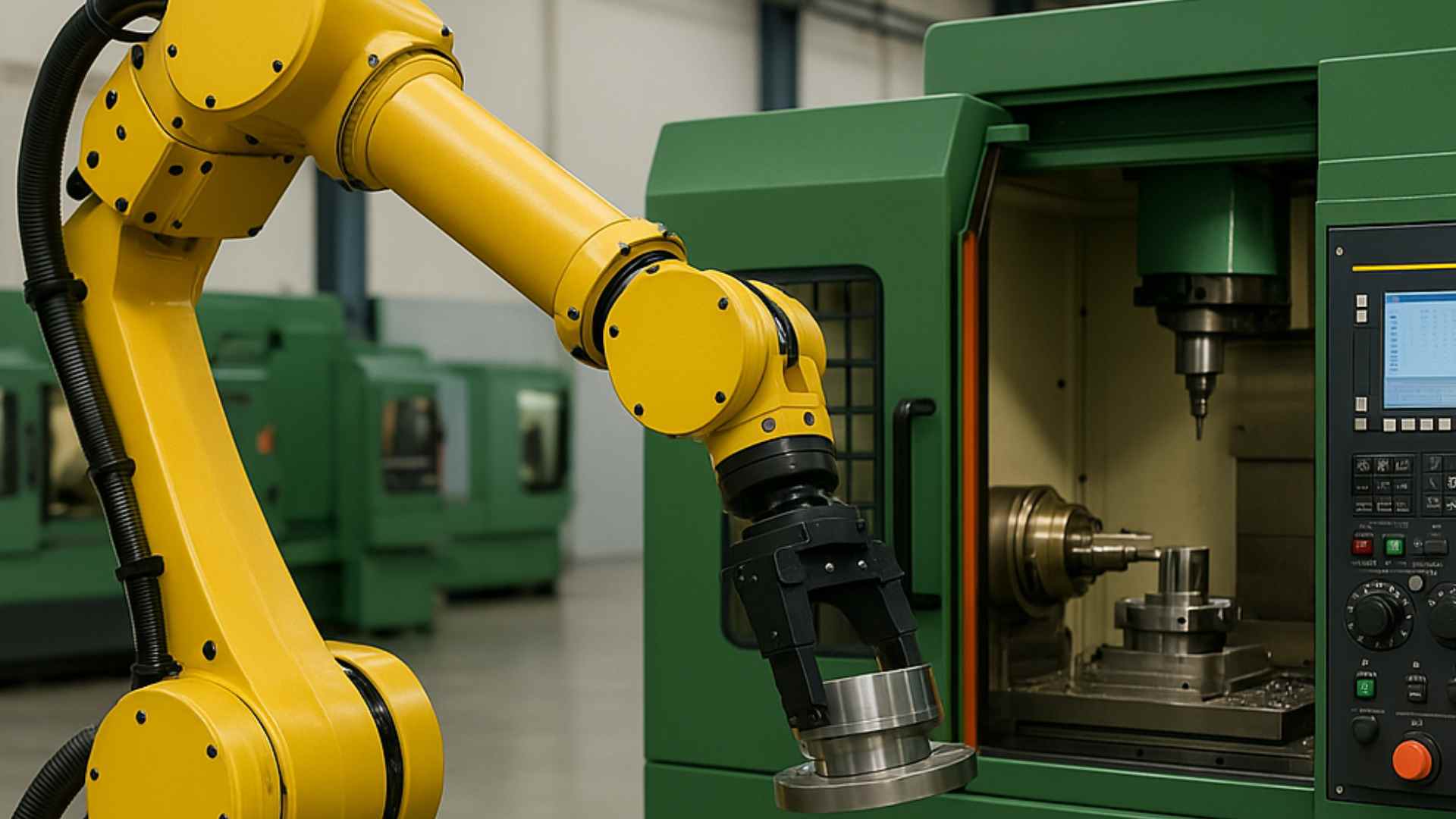
July 09, 2025
Share:
The era of smart manufacturing is well underway, and at the heart of this transformation is the integration of robotic arms with CNC (Computer Numerical Control) machines. Long gone are the days when CNC machining was solely reliant on manual loading, unloading, and part handling. With the help of robotic automation, manufacturers are now achieving higher throughput, lower error rates, and significantly enhanced workplace safety.
In this blog, we’ll explore how robotic arms are revolutionizing CNC machine automation, their benefits, practical applications, and what the future holds for this powerful collaboration.
The Evolution of CNC Machine Automation
CNC machines have been central to modern manufacturing for decades. They offer unmatched precision, repeatability, and control over the machining of parts from metal, plastic, or composite materials. However, they’ve traditionally required significant human intervention—particularly for material loading/unloading, part repositioning, and inspection.
This dependence on manual labor presented several challenges:
- Limited operating hours
- High labor costs
- Increased risk of workplace injuries
- Inconsistent cycle times due to human error
Enter robotic arms—a game-changing solution that eliminates these bottlenecks and takes CNC machining to the next level.
What Are Robotic Arms in CNC Automation?
Robotic arms, also known as industrial manipulators or robotic loaders, are programmable machines designed to mimic human arm movements with high degrees of flexibility and accuracy. When integrated with CNC systems, they take over tasks such as:
- Loading raw materials
- Unloading finished parts
- Cleaning or deburring components
- Tool and pallet changes
- Quality inspection using vision systems
They’re often mounted beside CNC lathes, mills, grinders, or multi-axis machines and can be adapted to perform a wide variety of repetitive tasks.
Key Benefits of Robotic Arms in CNC Automation
1. Increased Productivity
Robotic arms work tirelessly—24/7 without breaks. They can dramatically reduce cycle times, eliminate idle periods between machining tasks, and support unattended or “lights-out” manufacturing, where machines operate overnight without human supervision.
2. Improved Precision and Consistency
Manual loading can result in slight inconsistencies in part placement, leading to machining errors. Robotic arms offer exact, repeatable positioning every single time, improving quality and reducing rework or scrap rates.
3. Enhanced Worker Safety
By taking over dangerous or repetitive tasks, robotic arms reduce the risk of injuries from sharp tools, heavy lifting, or exposure to metal shavings and coolants. This leads to a safer, healthier workplace environment.
4. Lower Operating Costs
While the initial investment in robotics may seem high, the long-term savings in labor, downtime, and rework justify the cost. Fewer errors mean less waste, and faster throughput drives higher profitability.
5. Greater Flexibility
Modern robotic arms are highly programmable and can be reconfigured to suit various parts, machines, and workflows. With quick-change grippers and smart sensors, they adapt to dynamic production demands without extensive downtime.
6. Seamless Integration with Smart Factories
Robotic arms can be connected to IoT platforms, vision systems, and cloud-based monitoring tools. This enables real-time data collection, predictive maintenance, and remote supervision—key components of Industry 4.0.
Common Use Cases in CNC Automation
- Machine Tending: Robotic arms load and unload parts into CNC machines with high speed and precision.
- Part Sorting and Packing: Once machined, parts are sorted and packed for shipment using robotic handling.
- Automated Inspection: Cameras and sensors mounted on robotic arms perform dimensional and surface inspections.
- Multi-Machine Tending: A single robotic arm services multiple CNC machines, maximizing utilization.
- Palletizing: Finished parts are arranged on pallets by robotic arms for easier transportation or further processing.
Real-World Example: Robotic Arms in a CNC Shop
Consider a mid-sized automotive parts manufacturer using CNC lathes to produce brake components. Initially, human operators manually loaded the blanks and removed the finished parts—leading to bottlenecks and inconsistent cycle times.
After integrating a 6-axis robotic arm with grippers, the company achieved:
- 40% increase in output
- 70% reduction in labor costs for that task
- 0 unplanned downtime during night shifts
- Higher product quality and customer satisfaction
This example illustrates how robotic CNC automation is not just for large-scale operations—it can benefit small and medium enterprises (SMEs) too.
Challenges of Robotic Arm Integration
Despite the many advantages, integrating robotic arms into CNC workflows is not without hurdles:
- High Initial Costs: While ROI is typically strong, the upfront investment can be daunting for smaller manufacturers.
- Programming and Training: Operators and engineers need training to program and maintain robotic systems.
- Compatibility Issues: Older CNC machines may not easily integrate with robotic systems, requiring retrofitting.
- Complex Setup: Custom grippers, sensors, and safety systems may need to be tailored for each application.
However, with advancements in collaborative robots (cobots), plug-and-play solutions, and user-friendly interfaces, these challenges are gradually diminishing.
The Rise of Collaborative Robots (Cobots)
An exciting trend in CNC automation is the rise of cobots—robots designed to work alongside humans safely. Cobots are:
- Easier to program
- More affordable
- Lightweight and flexible
- Equipped with safety features to stop when in contact with humans
They’re ideal for low-volume, high-mix production environments, enabling even small job shops to adopt automation.
The Future of CNC Automation with Robotics
The future looks incredibly promising:
- AI-powered robotic arms will adapt to changes in parts and tools without reprogramming.
- Vision-guided robotics will enable better part recognition, orientation, and quality inspection.
- Digital twins will simulate robotic workflows for optimization before physical deployment.
- Modular robotic systems will be reconfigurable, allowing shops to scale and diversify easily.
In essence, robotic arms are becoming indispensable partners in modern machining environments—transforming CNC automation into a smarter, faster, and safer process.
Explore More from Sahil Machines
Looking to discover more about CNC automation and industrial solutions?
FAQ
Yes, robotic arms can often be retrofitted to work with existing CNC machines, though integration complexity varies based on machine age and interface capabilities.
Not at all. With the advent of cobots and modular automation systems, even small and medium-sized shops can benefit from robotic CNC automation.
Depending on the application, robotic arms can boost CNC productivity by 30% to 50% or more by minimizing downtime and enabling continuous operation.
Rather than replacing workers, robotic arms augment human capabilities, taking over repetitive or hazardous tasks and allowing workers to focus on more strategic roles.
Many manufacturers see ROI within 12 to 24 months, especially in high-volume or multi-shift operations.
Follow Us:
Latest Posts
Get in touch with us about anything.
Connect with our team to explore the alloy solutions and machinery expertise you need.